|
Post by tileman2 on Aug 16, 2015 14:42:30 GMT -6
Been messing with cone 6 formulas for the last two years: they are more in line with my business model. Some initial results from my final recipe: Peak Temp: 2236F 2.30hr total ramp hold/s. Will have some run off tests here shortly. Well, it only took me a month to figure out how to post a pic. Tom
|
|
|
Post by tileman2 on Aug 16, 2015 14:54:26 GMT -6
My first attempt at controlling glaze run off: 40grams of glaze was used on the bottom side/w 3% Lithium. 2236F peak with 12 minute hold. You can see part of the catcher is dry: lost about 20%. Aluminum Oxide addition: .25%  However, somehow I managed to get the piece off sided on the catcher; ended up with glaze pooling on top:  Firing two bowls and a plate now: minor changes to the aluminum additions-- will see soon enough. Tom
|
|
|
Post by evan cornish-keefe on Aug 18, 2015 8:30:43 GMT -6
Hey tom, Without a full recipe the % additions aren't info I can decipher. I've been using only c6 glazes for the last year or two, some I fire to cone 4 or 5 depending on the clay body.
|
|
|
Post by tileman2 on Aug 18, 2015 22:28:54 GMT -6
Evan: There is nothing special about my cone 6 glaze recipe: usual frit, zno, and sio2. I use epk/bentolite as a glaze hardener, and 3& lithium carb. I fire to 2230F now; only because I want it just a bit more fluid so the colorants mix better. I decided to go to cone 6 for business reasons. I have complete turn around on a kiln in 24 hours, save 20-25% on electricity, and extend element life. The only unique issue with my glaze formula is purity levels: started buying zinc and silica outside of the normal ceramic biz channels. I have color samples in my studio which allows customers to pick out whatever they like. Here in the Midwest most choose solid colors: boring, but the final color is always the same- green-backs. I have made die cutters for all of my custom tile lines: can roll and cut tile two-three times faster than a press. Took me two years to develop a clay which does not require weighting, or stacking. Roll it, cut it, and when it reaches leather hard: flip it one time. I lose less than two percent in the entire process.  This is my personal favorite. Tom
|
|
Kuba
Full Member
 
SztukKilka in Old Formu
Posts: 111
|
Post by Kuba on Aug 19, 2015 10:25:08 GMT -6
Hi, Everybody (in some books  ) tells that at cone 6 it is impossible to grow big crystals. But I think this is an "urban legend"... I tried fire at ^6 and this is what I get with maximum 1222 C (2232F) and 3h of hold:  Same glaze on different shape:  The biggest problem is that crystals are very rough, especially where there is more glaze thickness. P.S. I like this green/turquoise very much:) More photos please.
|
|
|
Post by evan cornish-keefe on Aug 19, 2015 16:25:26 GMT -6
Nice turquoise Tom. I stopped using cone 10 glazes before getting very far with them, but it seems to me that cone 6 crystals can grow pretty quickly, say 3-4 inches in 4-6 hours- I'm not sure how that compares to cone 10 glazes?
There is so much possible variation among cone 6 crystalline glazes. I mostly use glazes with .15-.2 boron, and other flux ratio is like a cone 10 glaze, as is silica & alumina level in this case. Lithium and ff3110 aren't necessary.
I do find rough crystals, especially on flat surfaces. I hold between 1950 and 1750F and crystals get rough at the higher end and smooth into the glaze at the lower end. There's definitely more to that which I don't understand.
|
|
|
Post by tileman2 on Aug 19, 2015 17:48:49 GMT -6
Kuba- Evan: I have experimented with glaze applications from .75 down to .35 grams per Square Inch (SI). I have found that .40 up to .50 grams per SI produce the best results and minimize coarseness. I have also used as little as 1 percent lithium with more heat, and more lithium with less heat. The 3% at 2230F makes the glaze very fluid: which seems to help with crystal coarseness. Again, that is on flat surfaces: vertical surfaces would create a different variable. I do have a series of large format tile: 14 x 18 that I still use a cone 9 on because it accepts larger crystals without looking disproportionate. The cone 6 i use 2.5 hours total ramp time which gives me 2-2.5" crystals: which fit that size of tile. The reason I use a PH meter is to control hot and cold spots in the kiln. My top loader runs very hot in the lower right hand corner, and runs cold in the upper left hand corner. My PH normally runs 10.65 with 3% lithium: but in the lower corner I run it at 10.25 and in the cold spot, I run it up to 10.95. It does seem to help even out the results. The other trick I have learned is using roller rods under the large tile or platters. I mix an alumina, OM4, EPK and wollastanite clay mix through my 1/2 round die on my extruder: making 6" up to 16" round bars. I place a series of them under the large format tile, and large platters. It allows them to move without cracking: and it solved all the crazing problems I was experiencing because of drag. 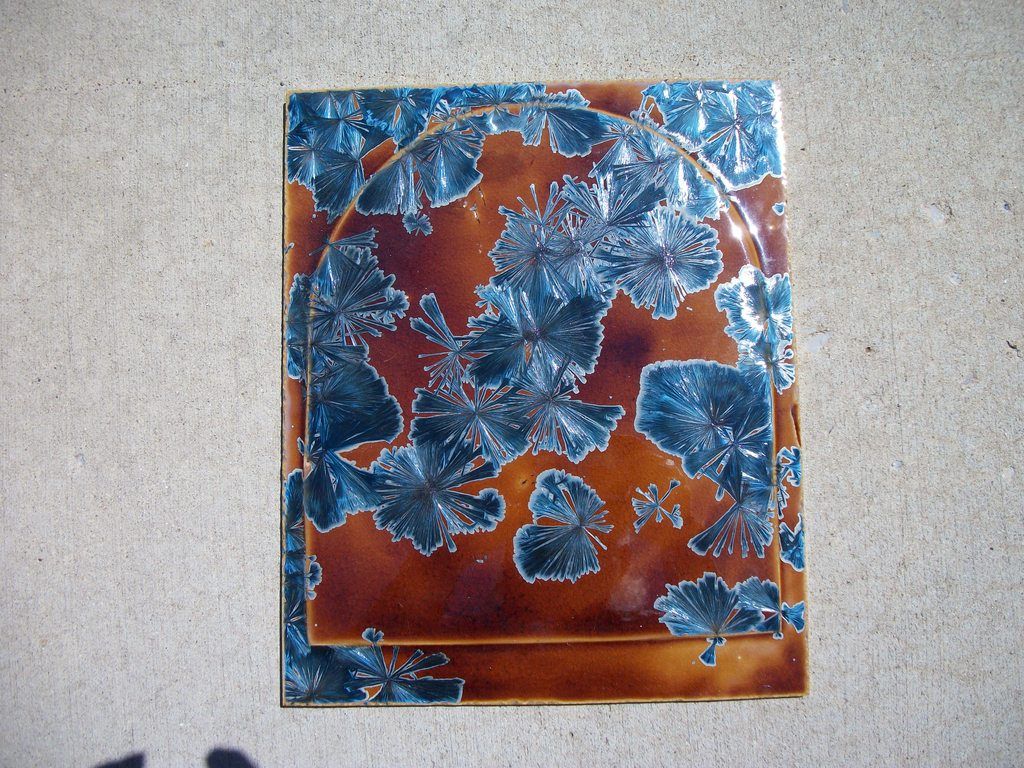 This is a large format tile I fire to cone 9. It is specifically designed for kitchen backsplashes. The standard height between the top of the countertop and the bottom of the upper cabinets is 13-14" This tile is 16" when it is finished: with the extra flat tabs it allows for the bottom and top to be trimmed so the pattern is directly centered. Tom
|
|
|
Post by tileman2 on Aug 20, 2015 18:55:18 GMT -6
Made my mother of 86 years a bowl in her favorite color. My second attempt at vertical pieces. Some rather odd crystal development on the right side. Cone 6- 2230F peak- 2.5 hrs ramp/holds. Clear glaze with .25% vandium. Guess I will have to start doing Islley's trick and drill an 1/8 hole in the bottom to let excess glaze run out. No catcher was used- bottom is a touch course due to excess glaze. 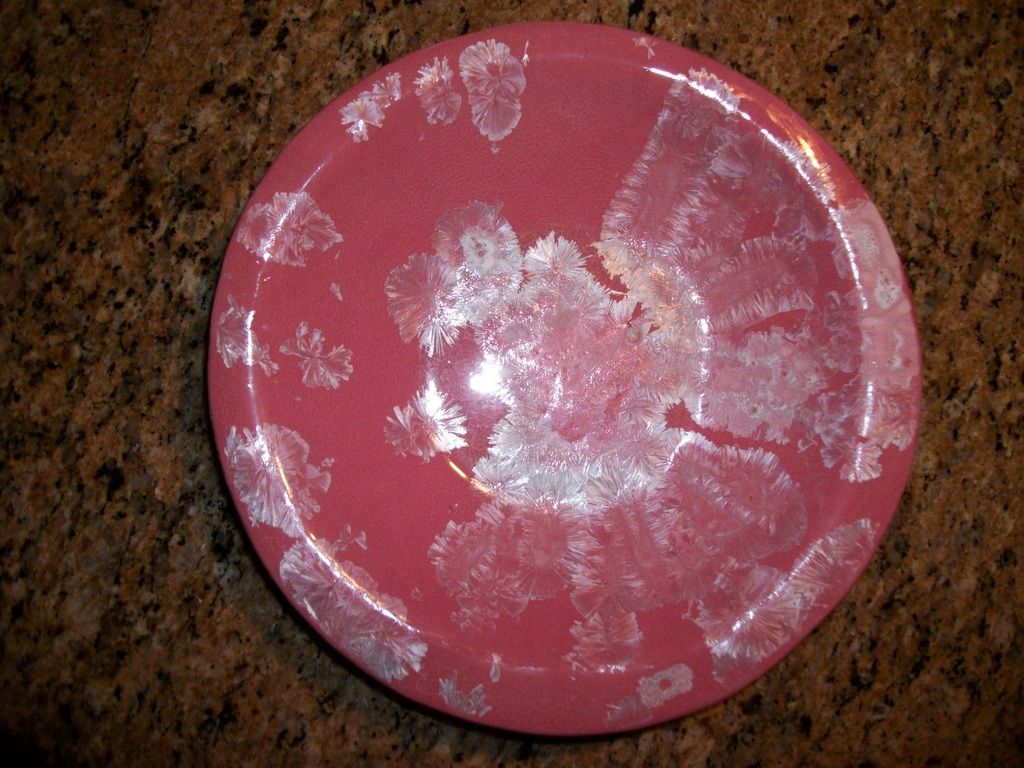 Tom Kuba--- love the cobalt- great crystal formation.
|
|
|
Post by tileman2 on Aug 20, 2015 19:16:23 GMT -6
Arnie: Posting this platter for you to illustrate a technique I learned when firing large format tiles. I explain it in the post above: using 1/2: round ceramic rods to sit the platter on so it can move while it is fired. After my last ramp hold, the kiln is off and naturally cools. I have not had any problems with crazing since I started using this technique. I did get this one a touch too hot; some minor boil off issues- cobalt and copper are more susceptible to it than the others.  Check out the bottom: it does have tiered sides. Tom
|
|
|
Post by Arnie Benton on Aug 20, 2015 19:59:59 GMT -6
Hi Tom -
I think if I used rods the bowls would sag - do you fire the bisque at a high temp or use a cone 10 clay so it doesn't sag? I've started using Silica sand - in the kiln now. It's not so hard to learn to apply the glaze so the middle doesn't pool. Making a hole in the bottom for me would mean I'd have to learn to make catchers ... which I have managed to avoid for all these years.
Arnie
Arnie
|
|
|
Post by tileman2 on Aug 21, 2015 13:11:13 GMT -6
I fire bisque to 1880F- touch higher than most. I made up several platters and bowls almost two years ago: just now getting around to firing them. I fired one at the time, absolute disaster, so I gave up on them until I developed a good cone 6 recipe. The clay was cone 6 porcelain that I slurried: added 10% molochite, some kyanite, and wollstanite too. Have no idea, but would guess a cone 7-8 clay body. Think I had 8-9 rods under the platter: spaced fairly close together. Was looking at the platter again today; actually I was wrong: bit too thin on bottom. I have a few platters and bowls made from cone 10 porcelain: will get around to frying them one of these days. Have several tile jobs to get done first.
Tom
|
|
|
Post by tileman2 on Aug 22, 2015 20:46:49 GMT -6
Jim:
Question to a confirmed once firer: I tried doing a once fire on my tile about two years ago. I saved a dozen pieces of greenware, and tried it again Friday for the second time. I applied glaze at .75 grams per SI- and it still absorbed most all of the glaze. What am I missing here?
Tom
|
|
|
Post by jfox on Aug 23, 2015 9:14:58 GMT -6
hard to say but some clays work better than others, try a heavier loading, then again putting to much glaze at one time will cause some clays to fail. Im hitting the road tomorrow morning
|
|
|
Post by evan cornish-keefe on Aug 23, 2015 22:56:11 GMT -6
I haven't noticed a correlation between rough crystals and glaze viscosity, the roughness is more extreme with thicker application (or horizontal) but seems to happen when thin just as frequently. The hold temperature seems significant, and the clay body seems to make a big difference. The bottom of this bowl has some very rough crystals protruding more than 1/8th inch from the surface, but also there are smooth crystals below the glaze surface at the bottom of the bowl, typical with this clay body (standards dark brown #266): 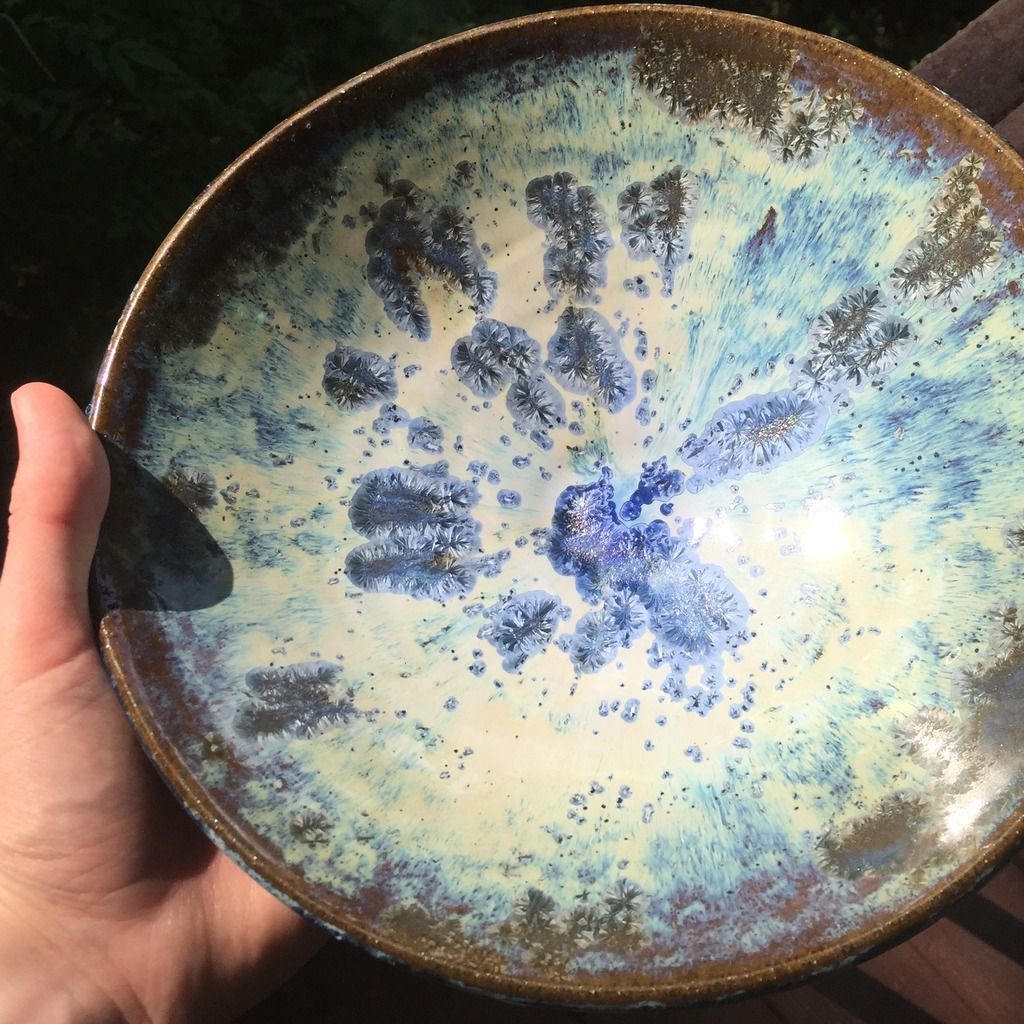
|
|
|
Post by tileman2 on Aug 24, 2015 18:04:55 GMT -6
Evan:
Interesting observation about hold temps: will have to go back through my firing schedules to check. I have been ramping between 1932-1936 for the most part: but have shot as high as 1950F (1084C). Will have to look into your theory- not thought about that aspect. By the way, what is the cut off temp before you stop adding 32 to C temps?
Tom
|
|